We provide comprehensive electrical testing services designed to ensure the safety, functionality, and efficiency of electrical systems in both residential and commercial settings. Our electrical testing services are essential for maintaining the integrity of electrical systems, preventing potential hazards, and ensuring that all installations are up to current electrical standards and regulations. By diagnosing problems early, we help our clients avoid costly repairs and minimize the risk of electrical failures.
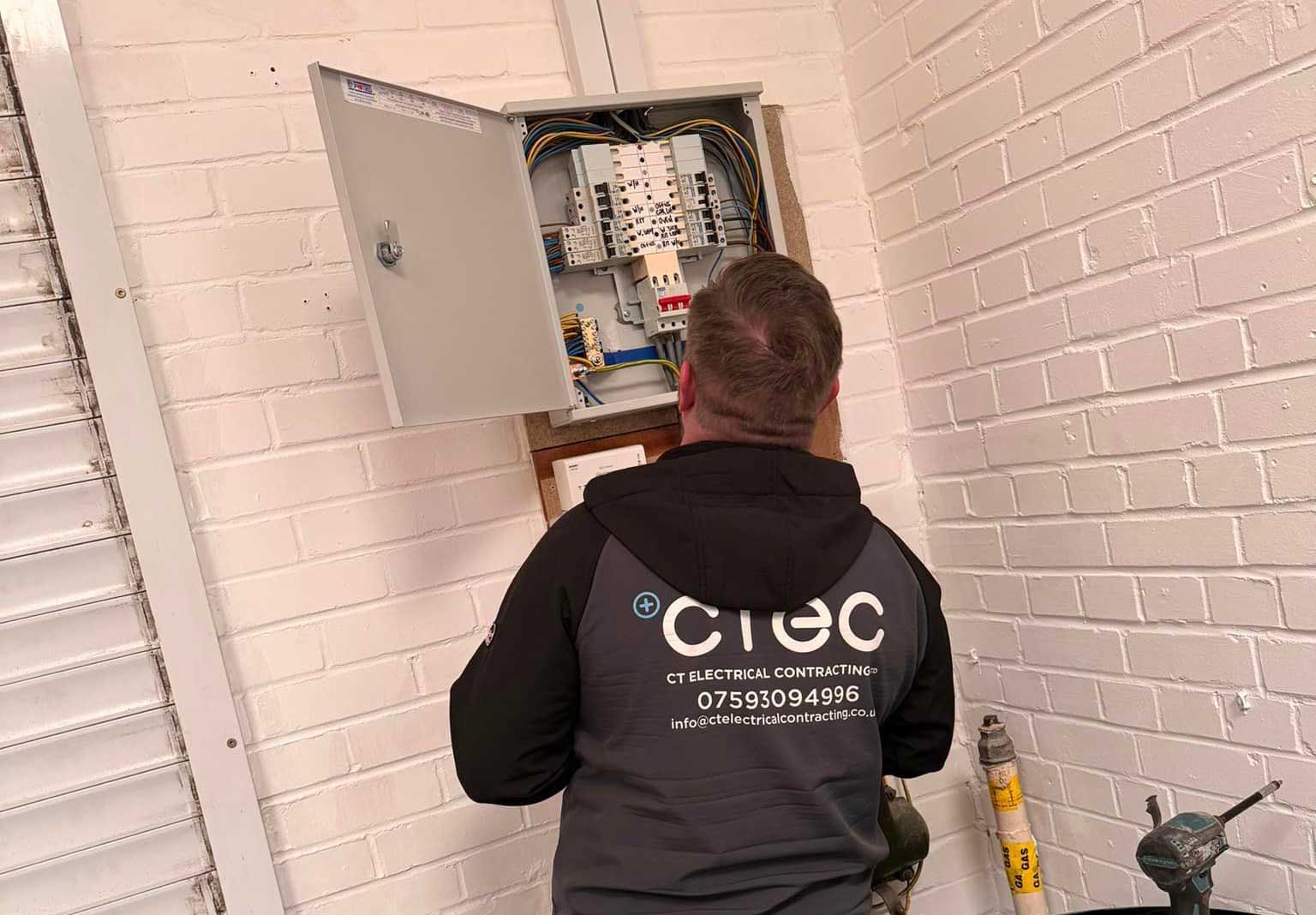
An EICR (Electrical Installation Condition Report) is a thorough inspection of your electrical installation.
The process involves a visual inspection of the electrical system, checking for damage and deterioration to the accessories and wiring, after the visual inspection we then carry out electrical tests on each and every circuit to get a suitable understanding of the condition of the electrical installation. At the end of the inspection, we will provide a full certificate detailing our findings which you can then provide to any necessary parties i.e. Insurance Companies, Mortgage Lenders, Estate Agents etc.
An EICR has two outcomes: Satisfactory, where the installation is good to go and ready for more years of service, or, Unsatisfactory, where the installation requires abit of TLC to bring it up to standards. In the event of an unsatisfactory test we will document all findings which will be attached to the certificate and will provide a free no-obligation quotation for the remedial work to be completed.
Landlord Test.
As a landlord, you will be aware that you’re responsible and legally obligated to maintain the electrical safety throughout the rental property. This includes the fixed wiring of the installation and any provided electrical appliances.
As of the 1st of June 2020, it is now a legal requirement that all rental properties should have an electrical inspection every 5 years or change of occupancy. Although there is no legal requirement it is also recommended that privately owned property should be tested every 10 years or on the sale of the property. These inspections, officially known as Electrical Installation Condition Reports or EICRs, are required to be carried out by a qualified, competent electrician.
Whether you're a homeowner wanting to ensure your property is safe or a business looking to comply with health and safety regulations, our experienced team is equipped to provide the detailed assessments and solutions you need.
Electrical Equipment Testing (EET) - Formally known as PAT testing
The term "PAT Testing" has been updated to "Inspection and Testing of Electrical Equipment" (ITEE) or Electrical Equipment Testing (EET). The testing criteria and procedures remain consistent. The name alteration aims to reduce confusion regarding what requires testing
What is EET Testing?
EET testing involves examining equipment and appliances to ensure they are safe for use. While not legally mandated EET testing is recommended as it helps comply with the requirement that all workplace electrical equipment must be maintained in a condition. It aids in identifying hazards and risks ensuring the safety of users and property.
CT Electrical will work with duty holders to ensure that your appliances are in line with the IET ‘Code of Practice for In-Service Inspection and Testing of Electrical Equipment’ and will provide an asset register of your appliances.
Testing includes:
- A visual inspection covering suitability of use, switching, wiring, connections and plug condition*
- Tests to verify earth continuity, polarity test, earth leakage test and insulation resistance
- Functional check of the equipment
- Identification of necessary repairs to the equipment
- In case an item fails the EET it must be taken out of service immediately. It should. Undergo repairs. Retesting or be replaced. Repairs need to pass a follow up test before the equipment can be put back into use.
- Issue of a test certificate
Frequency of testing
There are no guidelines regarding the timing of EET testing; it varies based on the risk level associated with the equipment, its usage and the work environment. The Health and Safety Executive offers recommendations, on testing schedules in their maintenance materials for both risk and low risk settings.
As a general guideline, Class I equipment should be tested every 48 months, whilst moveable equipment, such as extension leads and any portable electrical equipment, should be tested every 24 months. Handheld equipment should be tested every 12 months.
The insurance industry recognizes the process, and without up-to-date risk assessments or test certificates, insurance companies may invalidate your policy.
What Equipment Requires Testing under EET?
EET Testing is applicable to any equipment that is plugged into the mains power supply. This includes office devices such as phone chargers and computers household appliances like kettles and microwaves well as larger industrial machinery. Even if an item is not portable and is fixed or integrated into a system it still needs testing when connected to mains electricity. However items powered by batteries or cordless devices do not need testing; however their chargers should be tested.
The necessity of an EET stems from obligations for employers to ensure equipment safety as per the Electricity at Work Regulations 1989. The Health and Safety at Work Act 1974 also requires employers to safeguard their employees health, safety and welfare. While PAT or EET testing isn't mandatory by law it is advisable, for identifying and managing risks to maintain equipment safety.